After taking a brief pause to repair the transmission in his other Honda, JP returned to tackle engine 4316. One recurring issue with oil pans is over-tightening, which warps the sealing surface—and this one was no exception. However, the pan had an additional problem: a previous repair attempt with epoxy to fix a leak. Ultimately, we had to source a replacement pan from the parts bin.
Restoring the Oil Pan
The damaged pan with the epoxy repair was set aside, and we retrieved an NOS (new old stock) pan from storage. Unfortunately, water had pooled in the NOS pan during storage, leading to light corrosion. After cleaning and prepping, we replaced the rear cover gasket and fitted a new gasket and rear seal from Ortmann, ensuring everything was ready for the flywheel assembly.
Starter Repairs and Replacement Challenges
The starter, though outwardly in poor condition, worked surprisingly well. However, it had a circlip that was too large and needed replacing. Additionally, the supplied O-ring from the Ortmann kit seemed to be the wrong size, likely due to mishandling by a previous shop.
Other parts posed challenges, too. For example, the thrust washer sourced from CMSnl was mislabeled as 27mm but measured 25mm. We had to acquire replacements from Colin to proceed.
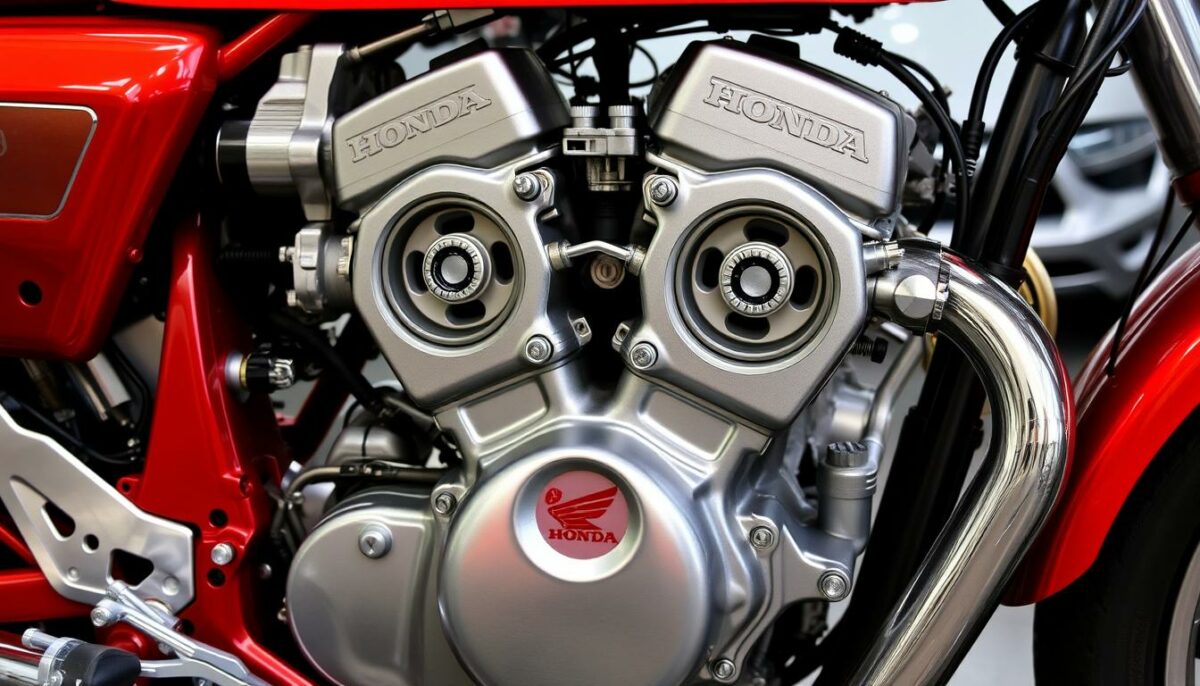
The Story of Shoreham’s Matching Numbers Engine
The body of Shoreham was fully restored, but its matching numbers engine languished for over two years in a restorer’s shop. During this time, numerous parts mysteriously vanished—some even after replacements were ordered. Persistent delays, a subcontractor shop fire, and countless calls eventually led to the engine’s retrieval. Disheartened by this ordeal, we moved 4316 and three other engines to JP for proper restoration.
This experience inspired me to write about how to select a reliable engine restorer. Shoreham’s engine rebuild required meticulous attention since it started as disassembled components in boxes—many untagged and damaged by improper handling.
Challenges in Restoration
Restoring engine 4316 revealed numerous challenges:
- Missing and Damaged Parts: Many components were lost or damaged. For instance, pistons #3 and #4 were severely scored, requiring oversized replacements.
- Improper Cleaning: Scotch-Brite wheels were overzealously used to clean gasket surfaces, leading to breaches in critical areas. These had to be corrected with epoxy and careful lapping.
- Fastener Issues: Incorrect bolts had been used in several places, causing structural damage that required repair.
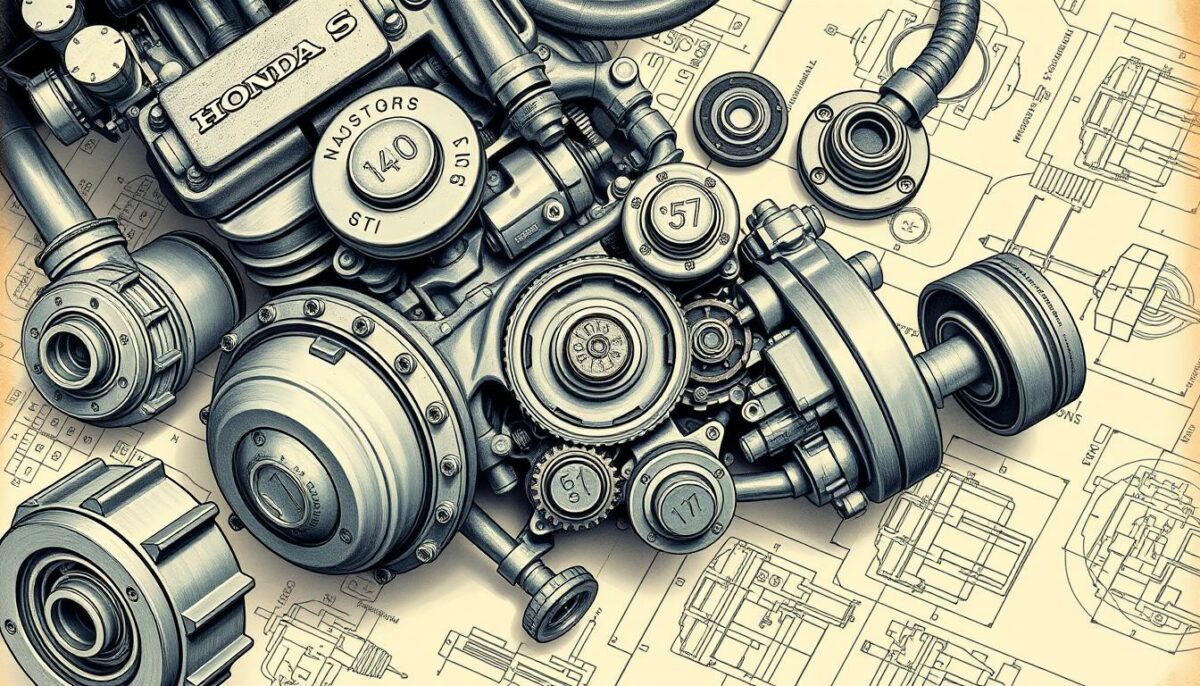
Progress and Precision
Combustion Chambers and Valve Work
During the restoration, we discovered the head was slightly warped, likely from overheating—a factor contributing to the engine’s original failure. The valves were re-lapped, and the combustion chambers were carefully smoothed to ensure optimal performance.
Intake Manifold Restoration
The intake manifold received much-needed attention, transforming it from a neglected state to pristine condition. New studs were installed after addressing issues with incorrect sizing.
Lifter and Camshaft Assembly
Cracked lifter cups were replaced, and shims were used to achieve the correct cam clearance. The head was cleaned and prepped, and critical dimensions on the crankshaft were verified for tolerance.
Lessons Learned
This journey underscored the importance of restoring parts rather than replacing them to maintain authenticity. Engine 4316, as Shoreham’s matching numbers engine, required extra care to preserve its historical significance. While the process revealed many frustrations from prior mishandling, each step brought us closer to breathing life back into this remarkable piece of engineering.
Stay tuned for updates as assembly progresses, and we bring Shoreham’s engine back to life, honoring its legacy with precision and care.